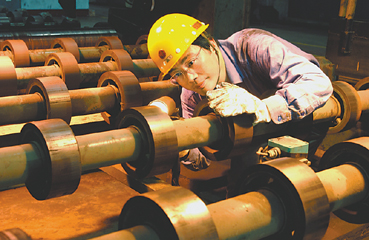
图为王军在工作中。
一个人,一个项目,三年便创造直接经济效益1.6个亿。
这个人叫王军,来自宝钢股份热轧厂,是一位高级技师,他负责的这个项目名为“高强度全密封热轧矫直机支承辊技术”。
这个项目打破了依赖进口或仿制外国产品的局面,通过技术转让先后在马钢、益钢不锈钢、SKF等企业推广,广受好评。这也让王军获得了2007年度国家科技进步奖二等奖。
科技创新是全民族的事业,“小人物”王军,这位由普通的岗位辅助工成长起来的新时代优秀智能型工人,登上了国家科技领奖台,向社会展现了新时代技能型、知识型工人的新风貌。
创新的起点在于一连串的“如果”
1987年9月,王军从宝钢技工学校毕业,成为宝钢热轧厂精整分厂生产综合作业区的一名剪刃组装工。
那个时候,进了宝钢,等于捧上了“铁饭碗”。加之高中毕业后读了两年技校,既有理论知识又有专业技能,王军应付现场的活儿已绰绰有余,一般人可能会就此停步了。可王军不一样,尽管他还并不明白创新是怎么回事。
1989年,王军所在的热轧生产线处于开工调试阶段。每天,他都早早赶到现场,有活干活,没活的时候,就跟在外方专家后面,问这问那。同样是装配剪刃,别人都是外方专家怎么说就怎么干,可王军却总要多问个为什么。一次,王军等8人用了整整一天,总算将一个机架的剪刃装好了,大伙儿正准备下班回家,可外方专家却告知,由于设计的原因,白天装的机架有问题,必须马上返工。
下班回到宿舍的王军躺在床上,两眼望着天花板,脑海中反复出现了一连串的“如果”:如果能看出设计缺陷,就可以避免装错;如果把整体性的组装化整为零,就用不着整体返工……
这些“如果”让王军第一次意识到,光凭自己在技校里学的知识,要想把“如果”变成现实,是绝对不够的。只有不断学习,才能提高技能,把工作做好。
剪刃组装看似体力活,其实有较高的技术含量,比如剪刃更换速度与装配质量,就与生产密切相关。勤学好问的王军早早地了解了剪刃装配质量对生产的重要性,一次,作业线按计划更换剪刃后发现,钢板剪切质量不如人意,虽经几次调整,效果仍不理想。年轻的王军主动请缨,在向生产方了解当班生产的产品规格后,轻松地在机架上调整了几个螺丝,开机一试,剪切质量果然达到了生产要求。
更换剪刃并非只是简单地将旧剪刃换下将新剪刃装上,它还牵涉剪切刀架的拆卸和安装,不仅工序复杂,而且劳动强度大,需要人手多。经过长期生产实践,王军的第一个创新成果《飞剪剪刃快速更换法》诞生了。
这个方法通过简化更换程序,既降低了劳动强度,又缩短了停机时间。以前更换一个剪刃,两个人需要一个半小时,采用王军的操作法后,一个人只用半个小时就行了。后来,这个工作方法被命名为宝钢集团公司先进操作法,并在七项先进操作法中名列榜首。
从此,王军用自己的一个又一个发明,告诉大家“辅助岗位也有技术含量”,并走上了一条创新之路。
创新的基础在于不懈地学习
其实,剪刃组装这个岗位工作量大,却只是现场生产的一个辅助工种。但王军进入剪刃班后,就一直没有因为是辅助工种而有想法,而是坚持自学成才。
结婚后的很长一段时间,王军一直住在很小的一居室内。由于喜欢读书,经常晚睡,为了不影响家人,善动脑筋的王军想出了办法―――把写字台、必备的资料和画图纸、搞设计的工具全部搬进不足三平方米的阳台,并取名“阳光书屋”,在那里,他常常苦学到黎明。
1996年,当许多人忙于下海挣钱的时候,王军却想着如何实实在在地学点东西,进一步提高技能。他结合工作实际,考取了同济大学。从1996年到2004年,经过8年艰苦努力,王军获得了同济大学“机械设计制造与自动化”专业的本科文凭,系统掌握了机械设计制造原理与机电一体化方面的专业知识。
这个过程中,王军还非常注重提升自己的岗位技能。他主动要求参加热轧厂举办的区域工培训,掌握了切边等岗位操作技能,不仅成为热轧厂首批拥有多个岗位操作证书的区域工,还连续两年在热轧专业技术工种操作比赛中获得第一名的好成绩,王军也因此被破格授予技师资格。
2001年,宝钢专业工种技能鉴定社会化后,王军又成为上海市技能鉴定培训中心的首批宝钢学员,并顺利通过了钳工高级技师资格考试。
学无止境。除了学知识、学技能外,对于诸如英语、计算机、动态模拟仿真、电脑辅助设计等专业知识,王军都刻苦学习。通过努力,他成了熟悉电脑软硬件知识的行家里手。
这一切,为他从“总结操作法”的创新到“科研攻关”腾飞打下了坚实的基础。
从总结操作法到科研攻关的腾飞
王军在大家眼里是个“精力充沛,工作勤奋,一拍脑袋就是一个先进操作法,专利一个接一个”的能人,他的成绩得到越来越多认可的时候,各种荣誉也接踵而至。2001年至2004年,他从一个默默无闻的年轻人逐渐成长为全国十大青年岗位能手、上海市工人发明家。
而此时的王军,知识和技术的积累,已经让他不满足于总结操作法,或是对设备进行小改革了,针对生产中的瓶颈问题,他开始走上科研攻关的道路。
获得国家科技进步二等奖的《高强度全密封精整矫直机支承辊技术》起源于2050热轧薄板线的一个国产化科研攻关项目。当时,由于剪切线矫直机支承辊的密封性不够好,每次更换支承辊或添加油脂后,都会形成油污板,导致产品被降级处理,造成较大的经济损失。工程技术人员通过国产化攻关,实现了支承辊的国内生产,但对支承辊密封结构的防尘和防泄漏问题一直未能解决。由于有关技术人员工作调动,中板及厚板线支承辊的国产化攻关一直未能进行。
2001年,王军接手中板及厚板线支承辊科研攻关任务,他在原有国产化攻关成果的基础上,根据不同板线装置的不同需求,以及生产条件的变更情况,对该技术进行了一系列科研攻关,在中板及厚板线成功开发了矫直机支承辊系列技术,他还与宽厚板厂技术人员合作,将该技术用到了宽厚板的冷矫直机上,产生了良好的效果。
实践证明,《高强度全密封精整矫直机支承辊技术》在不同生产线的推广应用,不仅满足了高强度板的生产需要,杜绝了油污板,实现了支承辊的免维护和可修复,提高了支承辊寿命和带钢表面质量,而且经济效益显著―――该项目截至2005年一共投入100万元,可去年一年产生的效益就高达5300余万元。此外,该技术还包含了12项专利,6项技术秘密。
就王军个人来说,在宝钢的20年里,由他实施的设备改造项目已累计创经济效益1000多万元,在这个过程中,他还取得了6项技术秘密、3项先进操作法,申报了14项发明专利。
俗话说,一花独放不是春,王军还有意识地把身边更多的人带动起来,共同进步、共同提高。2000年初,王军积极参与组织了“热轧厂发明创新协会”活动并担任副理事长。他将自己的心得体会毫无保留地讲给协会的每一个成员听,并主动指导和帮助他人总结经验和成果。
在他的带动下,协会成立当年,热轧厂创新工程就取得令人惊喜的成果――全年共申报先进操作法47项,申报专利21项,被国家受理11项,授权8项;申报技术秘密88项,年创效益5656.74万元。
在他的带动下,热轧厂许多人走上了岗位创新道路,近3年来,热轧厂创新成果始终名列宝钢分公司前茅,还有5名创新协会成员在2007年进入宝钢分公司个人创新业绩排行榜前10名。
|